Cookie settings

The search for the perfect piece of wood
Share details about a promotion, welcome customers, describe a product, or talk about your brand.
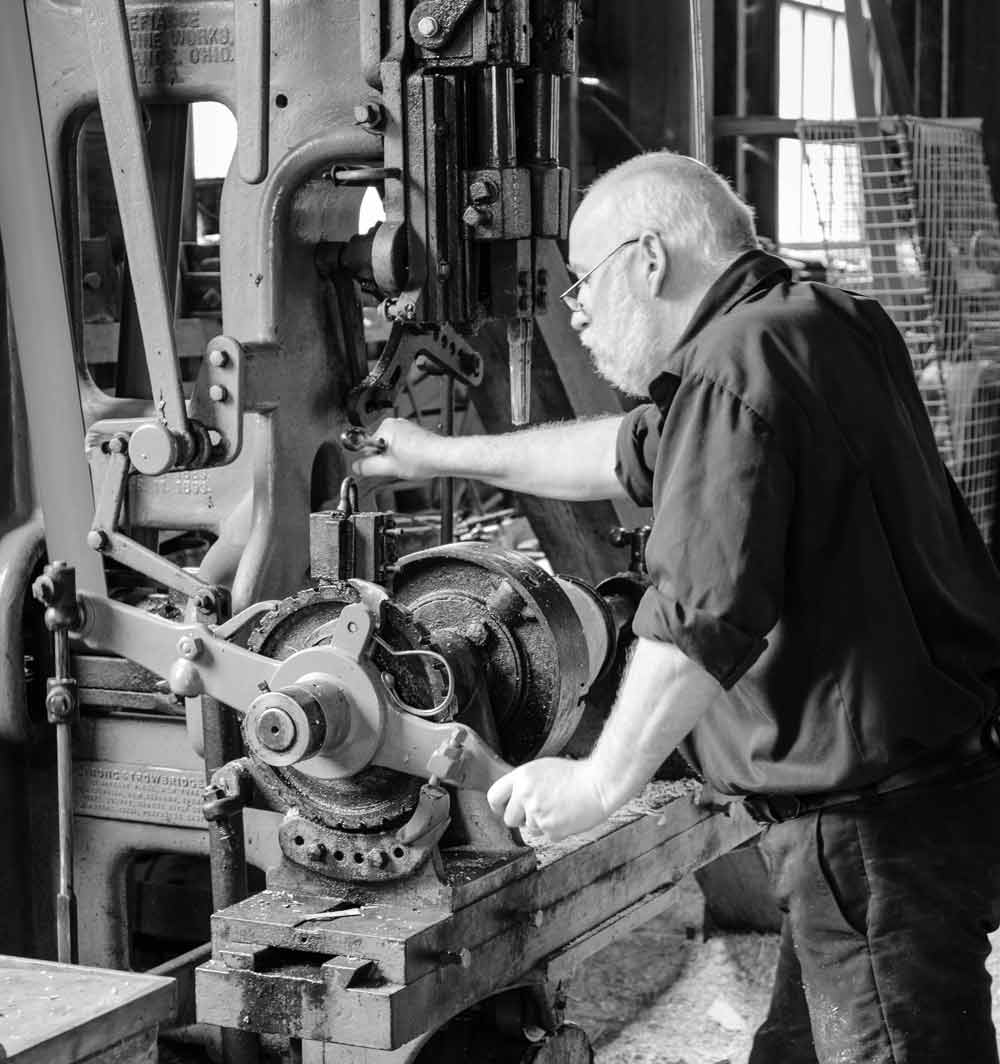
The brush shape is created
Share details about a promotion, welcome customers, describe a product, or talk about your brand.

Refining the brush shape
Share details about a promotion, welcome customers, describe a product, or talk about your brand.

Each hair type gets an individual pattern
Share details about a promotion, welcome customers, describe a product, or talk about your brand.

A unity is created between wild boar bristles and brush body
Share details about a promotion, welcome customers, describe a product, or talk about your brand.

Manual post-processing
Share details about a promotion, welcome customers, describe a product, or talk about your brand.
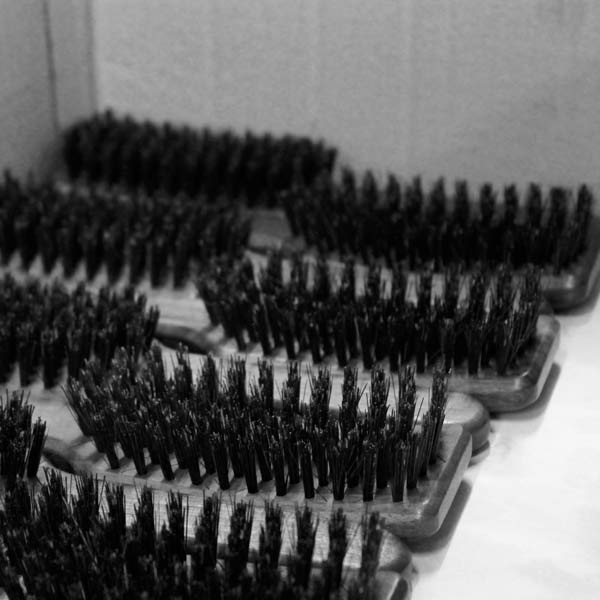
Final inspection
Share details about a promotion, welcome customers, describe a product, or talk about your brand.